Blog
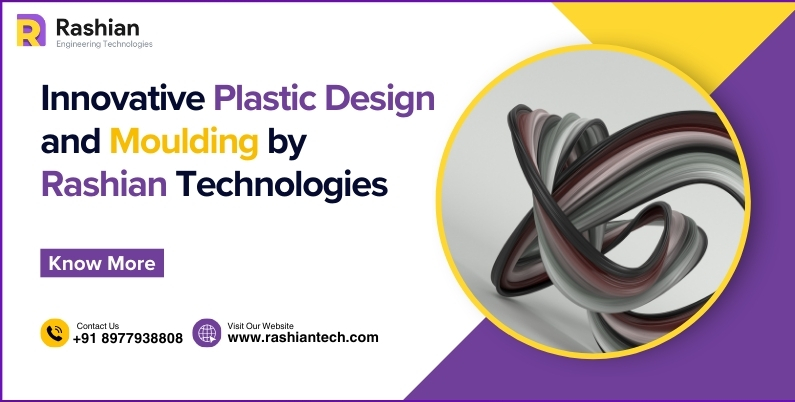
Innovative Plastic Design and Moulding by Rashian Technologies
In the modern manufacturing industry, the demand for high-quality plastic components is ever-increasing. Whether for automotive, consumer electronics, or industrial applications, the need for precision and reliability in plastic parts has become paramount. Rashian Engineering Technologies excels in this domain by offering cutting-edge plastic design and moulding services that ensure your components are developed with perfection.
Key Aspects of Rashian Technologies’ Plastic Design Services
- Plastic Part Design
Designing plastic parts requires more than just a basic understanding of molding processes. At Rashian Technologies, we focus on creating plastic parts that are not only functional but also optimized for manufacturability. Our design experts use advanced software and engineering techniques to develop parts that meet your specific application needs while minimizing material waste and production costs.
- Material Selection for Plastic Design
Choosing the right material for your plastic component is critical to ensuring its durability, flexibility, and performance in real-world conditions. Rashian Technologies provides expert guidance in selecting the appropriate material for your project based on factors like strength, thermal stability, and environmental impact. Whether you need a part that can withstand high temperatures or one that is resistant to chemicals, we’ll help you find the ideal plastic for the job.
- Processing Conditions for Plastic Molding
Achieving precision in plastic molding requires control over various processing conditions. From filling time and cooling time to shrink marks and gate filling contribution, our experienced team ensures every step of the molding process is optimized for quality. We take into account factors like tonnage, weld lines, and air traps to ensure your plastic parts are free from defects and meet the highest standards of performance.
Detailed information about the critical aspects of plastic moulding:
1. Filling Time
Filling time refers to the duration it takes for molten plastic to fill the mold cavity. This stage is crucial as it affects the overall quality of the final part. If the filling time is too fast, it can lead to defects such as flash (when excess material escapes from the mold). On the other hand, a slow filling time might cause incomplete parts or short shots. Optimizing filling time is essential for ensuring uniform material flow, minimizing defects, and achieving a high-quality finish.
At Rashian Technologies, we use sophisticated molding simulations to predict and optimize the ideal filling time for each project, ensuring that the molten plastic spreads uniformly across the mold cavity, resulting in defect-free products.
2. Weld Lines
Weld lines, also known as knit lines, occur when two flow fronts of molten plastic meet during the filling process. These are visible lines or weak spots in the molded part and are usually a result of the part’s geometry, the position of the gates, or the cooling pattern.
Weld lines can significantly affect the mechanical strength and appearance of the part. At Rashian Technologies, we address weld lines by optimizing the mold design, material flow, and processing conditions to minimize their occurrence. We ensure that the integrity of the part remains uncompromised, especially in high-stress areas.
3. Shrink Marks
Shrink marks are indentations or depressions that occur when the molten plastic cools and contracts inside the mold. These defects are common in thicker sections of molded parts where cooling is not uniform, leading to uneven contraction. Shrink marks can compromise the part’s appearance and dimensional accuracy.
To mitigate shrink marks, Rashian Technologies employs careful cooling time management, optimized gate placement, and a well-balanced mold design. We ensure even cooling and apply pressure where needed to minimize shrinkage and deliver parts with smooth surfaces and accurate dimensions.
4. Cooling Time
Cooling time is the period during which the molten plastic solidifies inside the mold. This is one of the most critical stages in the injection molding process since it significantly affects the cycle time and quality of the finished part. If cooling happens too quickly or too slowly, it can lead to warpage, distortion, or shrink marks.
Rashian Technologies carefully controls cooling time to ensure uniform solidification, preventing warping and maintaining the desired part geometry. We use advanced cooling system designs and simulations to balance the process, ensuring the optimal cooling rate for each project.
5. Tonnage
Tonnage refers to the amount of clamping force applied by the molding machine to keep the mold closed during the injection process. If insufficient tonnage is applied, the mold may open slightly under the pressure of the injected plastic, leading to flash. Conversely, applying excessive tonnage can damage the mold and increase wear and tear on the machine.
At Rashian Technologies, we carefully calculate the required tonnage based on the part’s size, geometry, and material. This ensures that the mold remains securely clamped during injection without compromising part quality or mold longevity.
6. Gate Filling Contribution
Gate filling contribution refers to the role the gate (the entry point for the molten plastic into the mold) plays in the overall flow of the material. The location, size, and type of gate can significantly affect how the plastic fills the mold cavity. Poor gate design can result in uneven flow, weld lines, or air traps, which can compromise part strength and aesthetics.
Rashian Technologies optimizes gate design and placement to ensure uniform filling and minimize flow-related defects. By controlling the gate’s contribution to the filling process, we can enhance part quality, reduce stress concentrations, and avoid common molding issues.
7. Air Traps
Air traps occur when air gets trapped inside the mold cavity as the molten plastic flows in. If not properly vented, these trapped air pockets can cause defects like burn marks (caused by compressed air heating up) or voids (hollow areas inside the part). Air traps can weaken the part structurally and result in poor surface finish.
At Rashian Technologies, we use advanced venting techniques and mold design strategies to eliminate air traps. This includes carefully positioned vents that allow air to escape as the plastic fills the mold, ensuring the material flows smoothly and fully into every part of the mold.
The Benefits of Choosing Rashian Technologies for Plastic Design
When you choose Rashian Technologies for your plastic design and molding needs, you benefit from our holistic approach to manufacturing. Here’s why we stand out:
- Expert Team: Our experienced engineers are well-versed in the latest plastic molding techniques and software, ensuring that your project is in capable hands from start to finish.
- Customization: We offer tailored solutions based on your unique requirements, ensuring that each plastic part is designed and manufactured to meet your exact specifications.
- Quality Assurance: Rashian Technologies is committed to delivering high-quality plastic parts with minimal defects. Every part we produce undergoes rigorous testing and quality checks to ensure it meets industry standards.
- Cost-Effectiveness: By optimizing the design and manufacturing process, we help you reduce production costs while ensuring high-quality results.
- Timely Delivery: We understand the importance of meeting deadlines, and our streamlined processes ensure that your parts are delivered on time without compromising on quality.
Applications of Rashian Technologies’ Plastic Design
Our plastic design services cater to a variety of industries, including:
- Automotive: High-strength and durable plastic components for automotive interiors, exteriors, and under-the-hood applications.
- Consumer Electronics: Precision-molded plastic parts for devices such as smartphones, tablets, and home appliances.
- Medical Devices: High-quality, sterile plastic components used in medical equipment and devices.
- Industrial Equipment: Durable and cost-effective plastic parts used in machinery, tools, and other industrial applications.
Conclusion
With a focus on precision, quality, and innovation, Rashian Technologies is your go-to partner for all your plastic design and moulding services. Whether you’re looking to develop a new product from scratch or optimize an existing design, our team is ready to assist you with the expertise and technology required to bring your vision to life.
Ready to get started? Contact Rashian Technologies today to discuss your plastic design project and experience the benefits of working with industry leaders in plastic design and moulding services
FAQ’s:
- What is plastic part design?
Plastic part design involves creating a detailed blueprint for a plastic component, focusing on factors like geometry, material selection, and moldability to ensure the part meets functional and aesthetic requirements.
- How does Rashian Technologies ensure quality in plastic molding?
- We use advanced simulation tools to optimize filling time, cooling time, and mold design, ensuring parts are free from defects like weld lines, shrink marks, and air traps.
- What are shrink marks in plastic molding?
- Shrink marks are surface depressions that occur due to uneven cooling or contraction of plastic. We minimize shrink marks by controlling cooling time and using precise mold designs.
- What is filling time, and why is it important?
Filling time is the duration for molten plastic to fill the mold cavity. Proper filling time ensures uniform flow and prevents defects like short shots or flash.
- How does Rashian Technologies handle air traps in the molding process?
We design molds with strategic venting systems to release trapped air during the injection process, preventing defects like voids or burn marks.
- What is gate filling contribution?
Gate filling contribution refers to how well the gate (entry point for molten plastic) controls material flow into the mold. Proper gate design ensures smooth flow, preventing issues like weld lines or uneven distribution.
- How do you reduce the occurrence of weld lines?
We optimize mold design and material flow patterns to minimize weld lines, which form when two flow fronts meet, ensuring the structural integrity of the part.
- What is tonnage in plastic molding?
Tonnage is the clamping force needed to keep the mold closed during the injection process. We calculate the appropriate tonnage based on the part’s size and material to prevent defects like flash.
- Why is cooling time critical in plastic molding?
Cooling time allows the molten plastic to solidify. Proper cooling ensures the part retains its shape and avoids warping or distortion.
- Does Rashian Technologies offer custom plastic molding solutions?
Yes, we offer fully customized plastic part design and molding solutions tailored to meet specific requirements in terms of material, geometry, and functionality.
13 comments on “Innovative Plastic Design and Moulding by Rashian Technologies”
Comments are closed