Blog
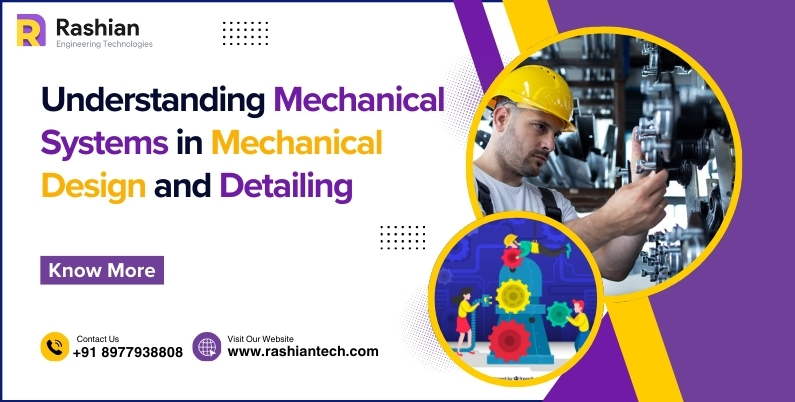
Understanding Mechanical Systems in Mechanical Design and Detailing
The process of Mechanical Design and Detailing (MDD) is crucial in ensuring that these systems function optimally, meet safety standards, and achieve the desired performance. Whether you are designing a new product, improving an existing system, or preparing a model for production, understanding the intricacies of mechanical systems within MDD is essential. In this blog, we will explore the importance of mechanical systems in MDD, the process of mechanical design, and the detailing required to bring an idea to life.
Mechanical systems in MDD
Mechanical Design and Detailing (MDD) is the process of creating detailed specifications for mechanical systems, ensuring that all parts function together seamlessly. This process encompasses the development of the concept, selection of materials, structural analysis, and finally, the creation of technical drawings and documentation that guide the manufacturing process.
While the design phase involves formulating the idea, conceptualizing components, and defining how they will work together, the detailing phase involves providing the precise information needed for the production or assembly of the product. MDD integrates principles from mechanical engineering, material science, and manufacturing techniques to produce efficient, safe, and reliable systems.
The Role of Mechanical Systems in Mechanical Design and Detailing
Mechanical systems refer to a combination of components that interact to perform a specific task or set of tasks. These systems are found in everything from simple household appliances to complex industrial machines. The primary goal in designing a mechanical system is to ensure that it operates efficiently, reliably, and safely while meeting the functional requirements.
In MDD, mechanical systems must be analyzed in terms of:
- Functionality: The system must meet the required performance standards. For example, in an HVAC system, the mechanical components should provide the necessary airflow and temperature control.
- Efficiency: The system should minimize energy consumption, reduce waste, and perform tasks using the least amount of resources possible.
- Durability: The materials and design should ensure that the system lasts for its intended lifespan without excessive maintenance.
- Safety: Proper design and material selection ensure that the system is safe for operation, adhering to industry standards and regulatory requirements.
Key Aspects of Mechanical Design in MDD
Mechanical design is the initial phase of creating a mechanical system. This stage involves conceptualizing and formulating the ideas that will shape the product or system.
- Conceptualization: The design process begins by identifying the purpose and function of the mechanical system. Engineers often create several concepts or prototypes, considering factors like efficiency, cost, and user requirements.
- Material Selection: Once the concept is developed, selecting appropriate materials is crucial. The material must possess the required strength, durability, weight, and heat resistance for the system. For instance, in automotive design, steel might be used for structural parts, while aluminum may be chosen for components requiring lightness.
- Stress Analysis: Before moving to the detailing phase, the design undergoes stress analysis to ensure that the system can withstand operational forces without failure. Engineers use tools like Finite Element Analysis (FEA) to predict how different parts of the system will respond to various forces.
- Prototype Development: In many cases, a prototype is built to test the design’s functionality. This hands-on approach allows engineers to identify potential problems and make necessary improvements before the final design is completed.
Detailing in MDD: Bringing the Design to Life
The detailing phase is where the abstract design concepts are transformed into actionable and precise instructions for manufacturing or assembly. This phase involves the creation of technical drawings and documentation that define the exact specifications for every component.
- Technical Drawings: These are the blueprints that provide all the necessary information for manufacturing the system’s parts. They include dimensions, tolerances, material specifications, and assembly instructions. Accurate technical drawings are critical to ensuring that every part fits together as intended.
- 3D Modeling: Advanced computer-aided design (CAD) software is often used to create 3D models of the system. These models allow engineers to visualize how the system will operate and interact. 3D modeling can help identify potential issues, such as interference between components, before physical prototypes are made.
- Component Specifications: In MDD, each part of the mechanical system needs a detailed specification. This includes information about the material, dimensions, tolerances, and any finishing processes required. These details are crucial for ensuring that each part fits properly and functions as intended when assembled.
- Assembly Instructions: Along with individual component specifications, assembly instructions are provided to guide the process of putting the system together. This ensures that all parts are assembled in the correct order and according to the correct specifications.
Challenges in Mechanical Design and Detailing
While mechanical design and detailing are essential for creating high-quality systems, the process comes with its challenges. These challenges include:
- Complexity of Systems: Designing and detailing complex mechanical systems, such as turbines or automotive engines, requires careful coordination among many components and subsystems. Any small mistake can result in operational inefficiency or system failure.
- Material Constraints: Finding the right balance between material cost, strength, and weight can be challenging. Engineers must also consider the availability of materials and their environmental impact.
- Precision: Mechanical detailing requires an extraordinary level of precision. Small discrepancies in dimensions or tolerances can result in parts that do not fit together properly, leading to costly delays and rework.
- Time Constraints: The pressure to meet deadlines while ensuring that designs are both functional and manufactural can lead to compromises. It is crucial to strike a balance between speed and accuracy.
How Rashian Technologies Can Help
At Rashian Technologies, we specialize in mechanical design and detailing, offering comprehensive solutions to meet the needs of various industries. With our expertise in CAD, CAE, and CAM technologies, we provide detailed and accurate designs that ensure the efficiency, safety, and durability of your mechanical systems. Our experienced engineers collaborate closely with clients to ensure that the designs are aligned with their vision and technical requirements.
Whether it’s creating a new product, optimizing an existing system, or providing precise detailing for manufacturing, Rashian Technologies has the tools, knowledge, and expertise to deliver exceptional results.
Conclusion
Mechanical systems are the backbone of many industries, from automotive and aerospace to manufacturing and energy. Understanding the intricacies of Mechanical Design and Detailing is crucial for engineers to create systems that perform reliably and efficiently. The design phase focuses on conceptualizing ideas and selecting appropriate materials, while the detailing phase transforms those ideas into actionable specifications for production.
At Rashian Technologies, we understand the importance of both the design and detailing processes and work tirelessly to ensure that every system we create is optimized for performance, safety, and durability. By integrating advanced technologies and engineering expertise, we help businesses bring their mechanical systems to life, delivering solutions that meet the highest standards of quality and precision.
If you’re looking for expert Mechanical Design and Detailing services, get in touch with Rashian Technologies today!