Blog
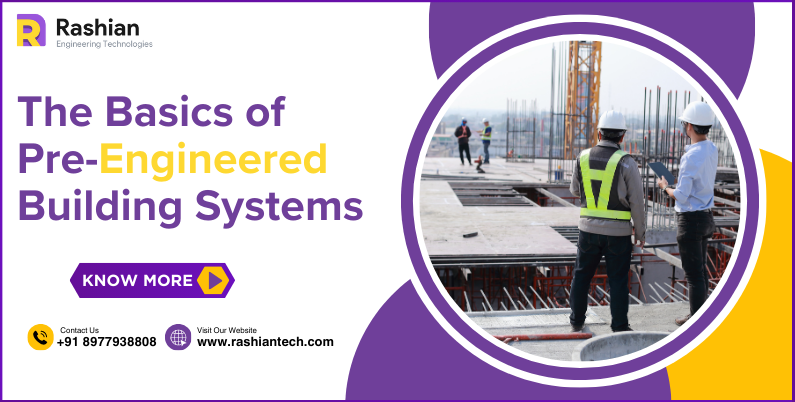
The Basics of Pre-Engineered Building Systems
The basics of Pre-engineered building systems represent a transformative approach to modern construction. Unlike traditional methods that involve building structures on-site from scratch, PEBs leverage advanced design and manufacturing techniques to create standardized components in factories. These components are then transported to the construction site for quick assembly, resulting in reduced timelines, costs, and environmental impacts,it is main basic of pre engineered building systems.
PEBs have emerged as a preferred choice in various sectors, including industrial, commercial, agricultural, and even residential projects. Their efficiency, flexibility, and sustainability make them a go-to solution for builders and developers worldwide. To understand the growing appeal of PEBs, it is essential to delve into their structure, components, and advantages.
Introduction to Pre-Engineered Building Systems
A PEB’s structural integrity lies in its meticulously engineered framework. These systems are typically designed using computer-aided tools to optimize the materials and ensure maximum strength and durability. The primary components of a PEB system include:
- Primary Frames: These are the main load-bearing elements, often made from steel. They consist of rigid frames, rafters, and columns designed to transfer loads efficiently.
- Secondary Members: Also known as purlins and girts, these components support the primary frames and provide additional stability. They also act as a base for the roofing and wall panels.
- Roof and Wall Panels: Typically made of metal, these panels provide the exterior skin of the building. They can be customized in terms of color, texture, and insulation properties to meet specific requirements.
- Fasteners and Accessories: Bolts, screws, and other fasteners are crucial for securing the structure. Accessories such as vents, doors, windows, and skylights enhance the functionality and aesthetic appeal of the building.
Each of these components is prefabricated in a controlled environment, ensuring consistent quality and precision. The components are then transported to the construction site, where they are assembled like pieces of a puzzle.
Design and Engineering Considerations
The design process for PEBs is highly efficient, thanks to advancements in engineering software. Structural engineers and architects collaborate to create designs that optimize material usage while meeting the client’s specifications. The designs are tailored to accommodate factors such as load requirements, local building codes, and environmental conditions.
A key feature of PEB systems is their modularity. This allows for easy customization and scalability. Whether it’s an industrial warehouse, a retail store, or an agricultural storage facility, the design can be adjusted to suit various dimensions and functionalities.
The use of lightweight materials further enhances the efficiency of PEBs. By reducing the overall weight of the structure, these buildings require less extensive foundations, which translates to cost savings and quicker installation times.
Advantages of Pre-Engineered Building Systems
One of the primary reasons behind the popularity of PEBs is the myriad of advantages they offer. These include:
- Speed of Construction: PEBs are designed and manufactured off-site, significantly reducing the construction timeline. Once the components arrive on-site, they can be assembled within weeks rather than months.
- Cost-Effectiveness: The efficient use of materials, reduced labor costs, and quicker construction timelines make PEBs a highly economical choice.
- Durability and Strength: Made from high-quality steel and other materials, PEBs are built to withstand harsh weather conditions, seismic activity, and other external stresses.
- Flexibility and Customization: The modular nature of PEBs allows for easy modifications and expansions. They can be designed to meet specific aesthetic and functional requirements.
- Sustainability: PEBs use recyclable materials and generate minimal waste during manufacturing and assembly. Additionally, they can be designed to incorporate energy-efficient features such as insulation and solar panels.
Applications of Pre-Engineered Buildings
PEBs are versatile structures that find applications across a wide range of industries. Some of the common uses include:
- Industrial Warehouses: PEBs provide large, unobstructed spaces ideal for storage and logistics.
- Commercial Buildings: Retail stores, showrooms, and office spaces benefit from the aesthetic appeal and cost savings of PEBs.
- Agricultural Facilities: From barns to grain storage, PEBs offer durable and spacious solutions for farming needs.
- Sports Arenas: Large-span PEBs are perfect for sports facilities, gymnasiums, and stadiums.
- Residential Projects: While less common, PEBs are increasingly being used for modern homes and multi-family housing developments.
- Cold Storage Facilities: PEBs can be equipped with insulation and climate control systems to create cold storage solutions for perishable goods.
- Educational Institutions: Schools, colleges, and training centers benefit from PEBs’ quick construction timelines and cost-effectiveness.
Challenges and Limitations
Despite their numerous advantages, PEBs are not without challenges. Some of the limitations include:
- Initial Design Costs: The upfront design process can be expensive due to the need for specialized software and engineering expertise.
- Transport and Logistics: Moving large prefabricated components to remote or inaccessible locations can be challenging.
- Standardization Constraints: While modularity is a strength, it may limit highly unique architectural designs.
- Maintenance: Steel components are prone to corrosion if not properly maintained, particularly in coastal or humid environments.
- Thermal Insulation Needs: Without proper insulation, PEBs can become excessively hot or cold depending on the external climate.
The Future of Pre-Engineered Buildings
The construction industry is constantly evolving, and PEBs are at the forefront of this transformation. Innovations in materials science, such as the development of corrosion-resistant alloys and advanced insulation, are further enhancing the capabilities of PEB systems. Additionally, the integration of smart technologies, such as IoT-enabled building management systems, is making PEBs more efficient and adaptable.
As sustainability becomes a top priority in construction, PEBs’ eco-friendly attributes will continue to drive their adoption. The ability to incorporate renewable energy systems, such as solar panels and rainwater harvesting mechanisms, aligns perfectly with the global push for green building practices.
The future also holds the promise of hybrid systems, where PEBs integrate with traditional construction methods to create structures that combine the best of both worlds. Advanced manufacturing techniques, such as 3D printing, may further revolutionize the production and assembly of PEB components.
Conclusion
Pre-engineered building systems are a game-changer in the construction industry. Their speed, efficiency, and versatility make them an ideal choice for a wide range of applications. While challenges remain, ongoing advancements in technology and materials promise to address these issues and unlock even greater potential for PEBs.
For businesses and individuals looking to invest in cost-effective and sustainable construction solutions, PEBs offer a compelling alternative to traditional methods. As the demand for efficient and eco-friendly buildings grows, pre-engineered systems are set to play a pivotal role in shaping the future of construction.
Frequently Asked Questions (FAQs)
1.What is a pre-engineered building (PEB)?
A: pre-engineered building is a structure where components are manufactured in a factory and assembled on-site. These buildings are designed to be efficient, cost-effective, and customizable.
2.How are PEBs different from traditional buildings?
A: Unlike traditional buildings, which are constructed piece by piece on-site, PEBs use prefabricated components. This approach reduces construction time, costs, and material waste.
3.What materials are used in PEBs?
A: PEBs primarily use steel for the framework, along with metal panels for roofing and walls. Insulation materials, fasteners, and accessories are also incorporated based on project requirements.
4.What are the primary applications of PEBs?
A: PEBs are used for industrial warehouses, commercial buildings, agricultural facilities, sports arenas, residential projects, cold storage facilities, and educational institutions.
5.Are PEBs environmentally friendly?
A: Yes, PEBs are considered environmentally friendly because they use recyclable materials, generate minimal waste, and can incorporate energy-efficient features like solar panels and insulation.
- PEBs be customized?
A: Absolutely. PEBs offer a high degree of customization, including dimensions, layouts, colors and additional features like skylights, doors, and windows.
7.How long does it take to construct a PEB?
A: The construction time for PEBs is significantly shorter than traditional buildings. Most projects can be completed within a few weeks, depending on the size and complexity.
8.What are the challenges of using PEBs?
A: Challenges include initial design costs, transportation logistics, and potential limitations in achieving unique architectural designs. Maintenance and insulation may also require special attention.
9.Are PEBs suitable for all climates?
A: PEBs can be adapted for different climates. Proper insulation and materials can ensure comfort and durability in both hot and cold regions.
10.What is the lifespan of a PEB?
A: With proper maintenance, a PEB can last several decades. High-quality materials and corrosion-resistant coatings further enhance durability.