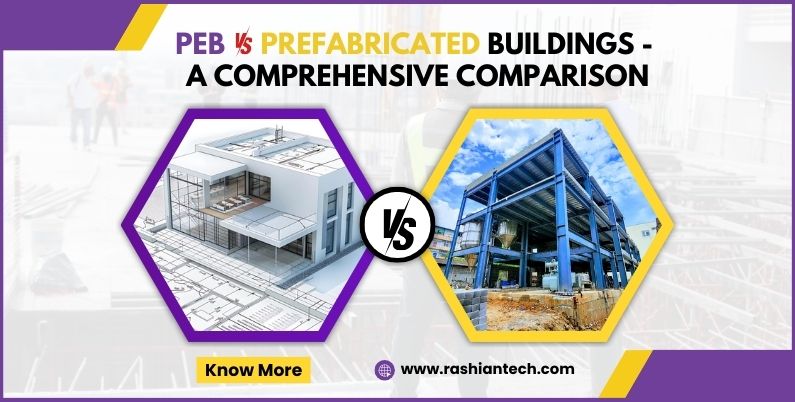
PEB vs Prefabricated Buildings – A Comprehensive Comparison
PEB vs Prefabricated Buildings – A Comprehensive Comparison
Pre-Engineered Buildings (PEB) and prefabricated buildings both revolutionize the construction industry by offering faster, more cost-effective alternatives to traditional methods, but they cater to different needs and applications. PEBs are highly specialized structures, primarily using steel or metal framing, that are custom-designed and manufactured in a factory setting before being quickly assembled on-site. This method is ideal for large-scale industrial and commercial projects due to its emphasis on structural integrity, durability, and customization. Contrariwise, prefabricated buildings encompass a broader range of modular construction techniques, utilizing various materials such as wood, concrete, and steel. These buildings can be standard or custom-designed and are assembled from pre-made components or modules, making them versatile for residential, commercial, and temporary structures. While both methods significantly reduce construction time and labor costs, PEBs excel in large, complex projects requiring robust structural solutions, whereas prefabricated buildings offer greater flexibility and a wider range of applications, check out for the basic PEB vs Prefabricated Buildings – A Comprehensive Comparison. Rashian Technologies specializes in both PEB and prefabricated solutions, ensuring that clients receive tailored, high-quality constructions that meet their specific needs and standards.
What is PEB?
Pre-Engineered Buildings (PEB) are structures that are designed and manufactured in a factory setting before being assembled on-site. This approach involves prefabricating building components such as columns, beams, and roof panels, which are then transported to the construction site for quick assembly. Here’s a more detailed overview:
Factory Fabrication:
Components are designed, engineered, and fabricated in a controlled factory environment. This ensures high precision and quality control.
Custom Design:
PEBs can be customized to meet specific requirements, including the size, shape, and functionality of the building. Design flexibility allows for adaptation to various applications such as industrial warehouses, commercial buildings, and sports facilities.
Modular Construction:
The building is constructed using modular components that are pre-engineered to fit together seamlessly. This modular approach reduces the amount of on-site work and speeds up construction time.
Speed of Construction:
Due to the pre-fabrication of components and efficient assembly process, PEBs can be erected much faster than traditional buildings. This leads to quicker project completion and earlier occupancy.
Cost-Effectiveness:
The factory-based production reduces labor costs and material waste. Additionally, the shorter construction time contributes to overall cost savings.
Durability:
PEBs are typically constructed using high-strength steel or metal framing, which provides durability and resistance to environmental factors. Properly maintained, PEBs can have a long lifespan.
Sustainability:
The use of efficient manufacturing processes and recyclable materials can make PEBs an environmentally friendly option. The reduced construction waste and energy-efficient designs contribute to sustainability.
Maintenance:
PEBs generally require low maintenance due to the quality of materials and precision in manufacturing. Regular upkeep is minimal compared to traditional buildings.
Applications of PEB:
- Industrial Buildings: Warehouses, factories, and distribution centers.
- Commercial Buildings: Retail stores, office spaces, and showrooms.
- Sports Facilities: Gyms, sports halls, and stadiums.
- Agricultural Structures: Barns, storage facilities, and greenhouses.
Benefits of Choosing PEB:
- Reduced Construction Time: Faster assembly on-site.
- Lower Costs: Economies of scale and reduced labor costs.
- High Quality: Controlled factory conditions ensure high standards.
- Flexibility: Customizable designs to fit various needs.
What is Prefabrication?
Prefabrication is a construction method where building components or entire structures are manufactured in a factory setting before being transported to the construction site for assembly. This process contrasts with traditional construction, where components are built and assembled on-site. Here’s a detailed overview of prefabrication:
Factory Production:
Components such as walls, floors, ceilings, and structural elements are prefabricated in a controlled factory environment. This ensures consistent quality and precision in manufacturing.
Types of Prefabricated Components:
Modular Units: Pre-built sections or modules that can be assembled on-site. These units often include pre-installed fixtures, fittings, and finishes. Panel Systems: Pre-fabricated wall or roof panels that are assembled on-site to create the building structure. Precast Concrete: Concrete elements such as beams, columns, and slabs that are cast in a factory and then transported to the construction site.
Design and Manufacturing: Components are designed according to project specifications and manufactured in a factory.
Transport and Assembly: Prefabricated components are transported to the construction site and assembled. This process is generally quicker than traditional construction methods.
Benefits of Prefabrication:
Speed: Prefabrication reduces construction time as components are built off-site and assembled quickly on-site.
Cost-Efficiency: Factory production minimizes labor costs and reduces material waste, leading to cost savings.
Quality Control: Manufacturing in a controlled environment ensures higher quality and consistency in components.
Reduced Site Disruption: Less on-site construction work minimizes site disruption and reduces the impact on surrounding areas.
Safety: Factory production can be safer than on-site construction, as many tasks are performed in a controlled environment.
Types of Prefabrication Systems:
Volumetric Prefabrication: Involves creating complete, three-dimensional modules or units that are assembled on-site.
Panelized Systems: Involves prefabricating flat panels (e.g., walls, floors) that are assembled into the building structure on-site.
Hybrid Systems: Combines prefabricated components with traditional construction methods for specific applications.
Applications of Prefabrication:
Residential Buildings: Prefabricated homes and apartments.
Commercial Buildings: Office buildings, retail spaces, and hotels.
Industrial Buildings: Factories, warehouses, and distribution centers.
Temporary Structures: Construction site offices, medical facilities, and disaster relief shelters.
Advantages of Prefabrication:
- Efficiency: Faster construction and reduced project timelines.
- Cost Savings: Lower labor costs and reduced material waste.
- High Quality: Controlled manufacturing conditions ensure consistent quality.
- Flexibility: Ability to customize and adapt designs according to specific needs.
Challenges of Prefabrication:
- Transportation Costs: Large prefabricated units can be costly to transport.
- Design Limitations: Certain design complexities may be harder to achieve with prefabricated components.
- Initial Investment: Higher upfront costs for factory production facilities and equipment.
Comparison between Pre-Engineered Buildings (PEB) and Prefabricated Buildings:
Aspect | Pre-Engineered Buildings (PEB) | Prefabricated Buildings |
Definition | PEB are structures designed and engineered in a factory setting, with components pre-fabricated for assembly on-site. | Prefabricated buildings are assembled from pre-made components or modules, often off-site, and then transported and assembled on-site. |
Design | Typically custom-designed for specific uses, with an emphasis on optimizing structural efficiency and functionality. | Can be standard or custom-designed; often modular, with predefined sections or modules. |
Construction Speed | Generally faster due to the precision of factory fabrication and efficient on-site assembly. | Also fast, but depends on the complexity of modules and assembly process. |
Cost | Cost-effective due to reduced construction time and factory-based fabrication, which minimizes labor and material waste. | Cost-effective depending on the modular approach and factory efficiencies, but can vary widely based on design and complexity. |
Material | Primarily uses steel or metal framing for structural elements, which can be pre-coated for durability. | Uses a variety of materials including wood, steel, concrete, or composite materials, depending on the module type. |
Flexibility and Customization | Offers flexibility in design and customization for specific structural needs, though based on a modular approach. | Modular design allows for customization but can be limited by the pre-defined module sizes and configurations. |
Durability | High durability with a focus on structural strength and resistance to environmental factors. | Generally durable, but longevity can depend on material quality and design. |
Sustainability | Often incorporates sustainable practices with efficient use of materials and energy in manufacturing. | Can be sustainable, especially if using eco-friendly materials and efficient production methods. |
Maintenance | Low maintenance due to high-quality materials and precise engineering. | Maintenance varies based on the materials used and the quality of the construction. |
Applications | Ideal for large-scale industrial, commercial, and warehouse buildings. | Suitable for a wide range of applications including residential, commercial, and temporary structures. |
Quality Control | High quality due to factory-based production and stringent quality controls. | Quality can vary based on the manufacturer and the level of factory control. |
Key Differences:
- Design and Engineering: PEBs are often designed with specific engineering goals in mind, focusing on efficiency and structural integrity. Prefabricated buildings can be more modular and standardized but may offer less customization.
- Material Usage: PEBs typically use metal or steel for structural elements, whereas prefabricated buildings can be constructed from a wider variety of materials including wood and concrete.
- Application: PEBs are commonly used for larger commercial and industrial projects, while prefabricated buildings are versatile and can be used for various types of structures, including residential.
Key Similarities:
- Speed of Construction: Both PEBs and prefabricated buildings are designed to accelerate construction timelines by reducing on-site work and leveraging factory-based fabrication.
- Cost-Effectiveness: Both methods aim to reduce costs through efficient production processes and minimized on-site labor.
Understanding these distinctions can help in choosing the right approach for your construction needs based on specific project requirements, budget, and design preferences.
Conclusion:
In the dynamic landscape of modern construction, PEB vs Prefabricated Buildings – A Comprehensive Comparison and Pre-Engineered Buildings (PEB) and prefabricated buildings both offer innovative solutions to traditional construction challenges. Each method brings its own set of advantages and considerations, and choosing the right approach depends on the specific needs and goals of a project. Pre-Engineered Buildings (PEB) are renowned for their rapid construction times, cost-effectiveness, and customizability. Designed and fabricated in a factory setting, PEBs are ideal for large-scale industrial and commercial applications where structural integrity and efficiency are paramount. Their use of metal framing and modular design contributes to durability, reduced maintenance, and a streamlined assembly process. Prefabricated Buildings, on the other hand, offer versatility in material use and design. They can range from modular units to panelized systems, making them suitable for a wide array of applications, including residential, commercial, and temporary structures. Prefabrication excels in speeding up construction and minimizing on-site labor, though its effectiveness can vary based on module design and transportation logistics.
At Rashian Technologies, we specialize in both PEB and prefabricated solutions, leveraging our expertise to deliver high-quality, efficient construction methods tailored to your specific needs. PEB vs Prefabricated Buildings – A Comprehensive Comparison and our commitment to innovation and excellence ensures that whether you choose PEB for its engineering precision or prefabrication for its modular flexibility, you will receive a product that meets the highest standards of performance and durability.
By understanding the key differences and benefits of PEB and prefabricated buildings, you can make an informed decision that aligns with your project requirements. Rashian Technologies is here to support you throughout the process, providing expert guidance and cutting-edge solutions to bring your construction vision to life.Explore how our advanced PEB vs Prefabricated Buildings – A Comprehensive Comparison can enhance your next project. Contact Rashian Technologies today to learn more about our services and how we can help you achieve your construction goals with efficiency and excellence.
13 comments on “PEB vs Prefabricated Buildings – A Comprehensive Comparison”
Comments are closed