Blog
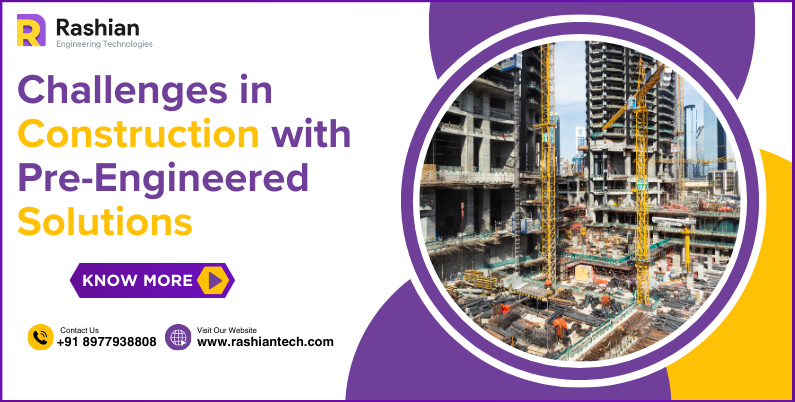
Challenges in Construction with Pre-Engineered Solutions: Exploring the Role of PEB Tech
In the ever-evolving construction landscape, Pre-Engineered Buildings (PEB) technologies have emerged as a game-changer. They offer a faster, more efficient, and cost-effective alternative to traditional construction methods. However, despite their numerous advantages, implementing PEB technologies in construction is not without its challenges. This article delves into these challenges, offering insights into how stakeholders can address them while maximizing the potential of PEB systems.
Understanding PEB Technologies
Pre-Engineered Buildings are factory-built structures designed to meet specific functional requirements. Components such as columns, beams, trusses, and panels are fabricated off-site and assembled on-site. These buildings are widely used for industrial warehouses, commercial spaces, aircraft hangars, and residential projects, thanks to their speed of construction, sustainability, and cost savings.
PEB technologies bring numerous benefits, including:
Speed of Construction: Pre-fabrication ensures quicker assembly, reducing project timelines significantly.
Cost Efficiency: Standardized designs and mass production lower material wastage and labor costs.
Design Flexibility: Advanced software allows for customized designs that suit various functional and aesthetic needs.
Sustainability: PEB components are recyclable, and the reduced construction waste contributes to eco-friendly building practices.
Despite these advantages, challenges persist in adopting and executing PEB technologies effectively.
Challenges in Construction with Pre-Engineered Solutions
Initial Investment and Cost Perception
While PEB systems promise cost savings over time, the initial investment can be higher than traditional construction methods. The use of advanced materials and specialized manufacturing processes often leads to apprehension among stakeholders who are focused on short-term budgets rather than long-term benefits.
Solutions:
Conduct cost-benefit analyses to highlight the lifecycle cost savings of PEB systems.
Educate clients and stakeholders about the long-term financial advantages, including reduced maintenance and operational costs.
Limited Awareness and Expertise
In many regions, there is a lack of awareness about PEB technologies and their applications. Additionally, finding skilled professionals with expertise in PEB design, fabrication, and assembly can be a challenge.
Solutions:
Organize training programs and workshops for architects, engineers, and contractors.
Partner with educational institutions to introduce PEB-related courses.
Leverage digital platforms to share success stories and case studies.
Transportation and Logistics Issues
Transporting large PEB components from the factory to the construction site can pose logistical challenges. Factors such as distance, road conditions, and component dimensions can lead to delays and increased costs.
Solutions:
Optimize component designs for easier transportation.
Use modular assembly approaches to minimize the size of transported parts.
Collaborate with logistics experts to develop efficient transportation strategies.
Customization Constraints
Although PEB systems are known for their design flexibility, achieving highly specific or unconventional architectural designs can be challenging. The standardized nature of PEB components sometimes limits creativity.
Solutions:
Invest in advanced design software that allows for greater customization.
Work closely with clients during the design phase to manage expectations and explore feasible solutions.
Combine PEB systems with conventional construction methods where unique architectural elements are required.
Regulatory and Compliance Issues
Meeting local building codes, safety standards, and zoning regulations can be a significant hurdle in PEB construction. Different jurisdictions may have varying requirements that complicate the design and approval process.
Solutions:
Engage with local authorities early in the project to understand regulatory requirements.
Employ compliance experts to ensure all standards are met.
Standardize PEB designs that align with common regulations to expedite approvals.
Environmental and Climate Considerations
PEB technologies must adapt to diverse environmental and climatic conditions. For instance, extreme temperatures, high humidity, or seismic activity can impact the performance and durability of PEB structures.
Solutions:
Use climate-specific materials and designs, such as insulated panels for thermal efficiency.
Conduct site-specific studies to determine environmental impacts and design adjustments.
Integrate renewable energy systems to enhance sustainability.
Maintenance and Durability Concerns
Some stakeholders worry about the long-term durability and maintenance needs of PEB structures. Misconceptions about the lifespan of pre-engineered components can hinder adoption.
Solutions:
Provide detailed maintenance guides and warranties to reassure clients.
Use high-quality materials and coatings that enhance durability and resistance to corrosion.
Regularly inspect and maintain structures to address wear and tear proactively.
Integration with Modern Technologies
The integration of technologies like Building Information Modeling (BIM), smart systems, and IoT with PEB systems can enhance efficiency and functionality. However, many firms lack the technological infrastructure and expertise to implement these solutions effectively.
Solutions:
Invest in BIM software and train personnel to use it.
Collaborate with tech firms to incorporate IoT and smart systems into PEB projects.
Use augmented reality (AR) and virtual reality (VR) tools for better design visualization and planning.
Supply Chain Dependencies
PEB construction heavily relies on a robust supply chain to deliver prefabricated components on time. Disruptions in raw material supply, manufacturing schedules, or transportation can significantly impact project timelines.
Solutions:
Develop multiple supply chain partnerships to ensure reliability.
Use digital tools for supply chain management and real-time tracking.
Maintain a buffer stock of critical components to avoid delays.
Cultural Resistance to Change
Traditional construction methods have been entrenched in the industry for decades, and convincing stakeholders to shift to PEB systems can encounter resistance. Cultural inertia and skepticism about new technologies often hinder adoption.
Solutions:
Showcase successful PEB projects to build confidence.
Involve stakeholders early in the decision-making process to address concerns.
Provide pilot projects or demonstrations to illustrate the advantages of PEB systems.
Opportunities in Overcoming Challenges
Addressing these challenges not only resolves existing bottlenecks but also opens up new opportunities for the growth of PEB technologies. Here’s how stakeholders can leverage these opportunities:
Market Expansion: Educating clients and governments about the benefits of PEB can unlock new markets, especially in developing regions where infrastructure needs are high.
Innovation in Materials: Investing in research and development of advanced materials can enhance the performance and versatility of PEB components.
Sustainability Leadership: Positioning PEB systems as a sustainable alternative aligns with global environmental goals, attracting eco-conscious clients.
Collaboration: Forming partnerships between PEB manufacturers, architects, and contractors can lead to more cohesive and successful project executions.
Digital Transformation: Embracing digital tools and technologies can improve design accuracy, streamline construction processes, and enhance project management.
Public-Private Partnerships: Collaborating with governments on large-scale infrastructure projects can accelerate the adoption of PEB technologies and establish industry standards.
Case Studies: Success Stories in PEB Technologies
Industrial Warehouse in India
A leading logistics company in India constructed a massive 100,000 sq. ft. warehouse using PEB technologies. By employing advanced design software and prefabricated components, the project was completed in a record time of six months. The client reported 30% cost savings compared to conventional construction methods.
Sports Complex in the Middle East
A sports complex in the Middle East utilized PEB systems to construct a high-capacity stadium. The use of climate-specific materials ensured thermal efficiency, while innovative design solutions addressed unique architectural requirements. The project showcased the adaptability and aesthetic potential of PEB technologies.
Commercial Office Building in the USA
In the USA, a tech firm opted for PEB technologies to build a sustainable office complex. Integrating solar panels and smart building systems, the project achieved LEED certification. This case highlights how PEB systems can align with green building standards.
Educational Campus in Africa
An educational institution in Africa employed PEB technologies to construct a campus in a remote location. The prefabricated components were transported and assembled quickly, overcoming logistical challenges and reducing overall project costs. This project demonstrated the viability of PEB systems in addressing infrastructural gaps in underdeveloped regions.
Conclusion
PEB technologies hold immense potential to revolutionize the construction industry. However, their widespread adoption depends on addressing challenges related to cost perception, expertise, logistics, customization, regulations, environmental factors, maintenance, technology integration, and cultural resistance.
By fostering collaboration, investing in innovation, and promoting education, stakeholders can overcome these hurdles and unlock the full benefits of PEB systems. As the demand for sustainable, efficient, and flexible construction solutions grows, PEB technologies are poised to play a pivotal role in shaping the future of the built environment.