Blog
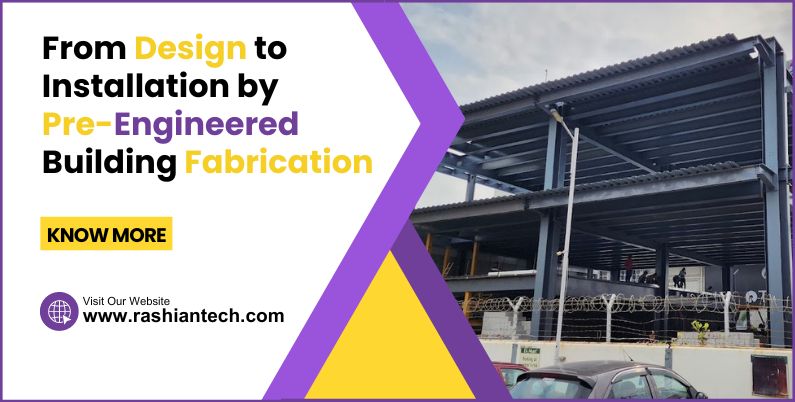
From Design to Installation by PEB
In today’s rapidly evolving construction landscape, pre-engineered buildings (PEBs) are gaining significant traction. Offering a blend of cost-efficiency, speed, and sustainability, PEBs are a modern marvel in the construction industry. This blog will take you through the journey from design to installation byPEB fabrication, highlighting the key benefits and processes involved.
From Design to Installation by PEB
Pre-engineered buildings (PEB) are structures built using a pre-designed and pre-fabricated steel framework. Unlike traditional construction methods, where each component is built on-site, PEBs are constructed off-site in a factory setting. This results in faster construction times, reduced waste, and often lower costs.
Different steps of the Pre-Engineered Buildings (PEB)
The Design Phase
The design phase is critical in ensuring that the pre-engineered building meets all client specifications and requirements. Understanding client requirements is a crucial initial step in the pre-engineered building (PEB) design process. It involves several key aspects:
- Purpose of the Building: Determining the primary use, such as retail, office space, or a combination of functions.
- Design Preferences: Identifying architectural styles, aesthetic preferences, and specific design elements desired by the client.
- Functional Requirements: Assessing space planning needs, load-bearing requirements, and potential future expansions.
- Budget Constraints: Understanding the financial limitations to create a cost-effective design.
- Regulatory Compliance: Ensuring that the design meets local building codes and regulations.
- Environmental Considerations: Factoring in sustainability goals and environmental impact.
- Timeline Expectations: Aligning the project schedule with client deadlines.
- Specific Amenities: Identifying required amenities like parking, accessibility features, and landscaping.
- Technological Integrations: Planning for necessary technological installations, such as HVAC, electrical systems, and smart building features.
- Client Feedback: Continuously incorporating client feedback throughout the design process to ensure satisfaction.
By thoroughly understanding these requirements, the design team can create a PEB that perfectly aligns with the client’s vision and operational needs.
2. Site Analysis
Site analysis is a critical step in the pre-engineered building (PEB) process, involving the thorough assessment of the construction site to ensure the building’s design and functionality align with the location’s characteristics. Key elements of site analysis include:
- Topography: Understanding the site’s terrain to address elevation changes and drainage needs.
- Soil Testing: Conducting geotechnical investigations to determine soil strength and composition, which affect foundation design.
- Climate Conditions: Assessing weather patterns, including wind, rainfall, temperature variations, and seismic activity.
- Accessibility: Evaluating transportation routes for materials and personnel, considering road access and proximity to infrastructure.
- Utilities: Identifying existing utilities like water, electricity, sewage, and communication lines, and planning for their integration into the building design.
- Environmental Impact: Analyzing the environmental implications, including flora, fauna, and potential pollution concerns, to ensure sustainable development.
- Zoning Laws: Reviewing local zoning regulations and building codes to ensure compliance with legal requirements.
3. Conceptual Design
Based on the client’s requirements and site analysis, a conceptual design is created. This includes:
- Architectural Drawings: Floor plans, elevations, and sections.
- Structural Design: Load calculations, foundation design, and structural framework.
- Mechanical, Electrical, and Plumbing (MEP) Design: Integration of HVAC, electrical, and plumbing systems.
4. Finalizing the Design
Once the conceptual design is approved, detailed drawings and specifications are prepared. This includes:
- Shop Drawings: Detailed drawings for each component to be fabricated.
- Bill of Materials: A comprehensive list of all materials required.
- Construction Schedule: A timeline for the fabrication and construction process.
5. The Fabrication Phase
The fabrication phase involves the manufacturing of the pre-engineered components in a controlled factory environment.
a. Material Procurement
High-quality materials are sourced based on the specifications provided in the design phase. Common materials include: Steel: For the primary and secondary framing. Insulation Materials: For thermal efficiency. Panels: Roofing and wall panels, which can be made from various materials like steel, aluminium, or composite.
b. Cutting and Welding
Using advanced machinery, the steel components are cut to precise dimensions. Automated welding processes ensure strong and consistent welds. Cutting and welding are crucial steps in the fabrication of pre-engineered buildings (PEBs), ensuring precision and structural integrity. Cutting involves using advanced machinery like CNC, laser, or plasma cutters to shape steel components accurately, reducing waste and ensuring perfect fits. Welding, often automated with robotic systems, joins these components using methods like MIG, TIG, or arc welding. High-quality welds are achieved through meticulous preparation and rigorous quality inspections, ensuring the final structure’s strength and durability. These processes collectively enhance efficiency, precision, and the overall quality of PEBs.
c. Component Assembly
Individual components are assembled into larger sections. This can include:
- Primary Framing: Columns, rafters, and beams.
- Secondary Framing: Purlins, girts, and bracings.
- Panels: Roof and wall panels are pre-fabricated and insulated.
d. Quality Control
A rigorous quality control process ensures that all components meet the required standards. This includes:
- Dimensional Accuracy: Ensuring all components are cut and assembled to exact specifications.
- Weld Quality: Inspecting welds for strength and consistency.
- Material Quality: Verifying that all materials meet the specified grades and standards.
6. The Transportation Phase
Once the components are fabricated, they are transported to the construction site. Packaging: Components are carefully packaged to prevent damage during transit. This can include protective coverings and secure strapping. Logistics: A logistics plan is created to ensure timely and efficient transportation. This includes route planning, scheduling, and coordination with transport companies.
7. The Installation Phase
The installation phase involves the assembly of the pre-fabricated components on-site.
a. Site Preparation
Before installation begins, the site is prepared. This can include: Foundation Work: Pouring concrete foundations or footings. Site Clearing: Removing any obstacles or debris. Leveling: Ensuring the site is level and ready for construction.
b. Erecting the Framework
The primary framework is erected first. This includes: Setting Columns: Placing and securing the steel columns. Installing Beams and Rafters: Connecting the beams and rafters to form the basic skeleton of the building. Bracing: Adding bracing for structural stability.
c. Adding Secondary Framing
Secondary framing components, such as purlins and girts, are added to provide additional support and structure.
d. Installing Panels
Roof and wall panels are installed to enclose the building. This includes:
- Roof Panels: Securing the roof panels to the purlins.
- Wall Panels: Attaching wall panels to the girts.
- Insulation: Adding insulation materials for thermal efficiency.
8. Finishing Touches
The final steps involve adding the finishing touches to the building. This can include: Doors and Windows: Installing doors and windows. Interior Finishes: Adding interior walls, flooring, and ceilings. MEP Systems: Installing and connecting mechanical, electrical, and plumbing systems.
Conclusion
In conclusion, the journey From Design to Installation by PEB Fabrication is a testament to the evolution of construction technology. Through meticulous planning and innovative design, pre-engineered buildings offer a streamlined and efficient approach to modern construction. Rashian Technologies plays a pivotal role in this process, providing cutting-edge solutions and expertise that enhance the quality and efficiency of pre-engineered buildings. Their commitment to technological advancement and customer satisfaction ensures that every project not only meets but exceeds expectations. By integrating state-of-the-art technologies with industry best practices, Rashian Technologies continues to set new standards in the field, transforming the vision of pre-engineered buildings into reality.
Pre-engineered buildings offer a revolutionary approach to construction, combining efficiency, cost-effectiveness, and sustainability. From Design to Installation by PEB Fabrication, every step is meticulously planned and executed to ensure a high-quality end product. By understanding the processes involved in pre-engineered building fabrication, clients can make informed decisions and enjoy the many benefits that PEBs offer.
FAQ’s
Q1: What is pre-engineered building fabrication?
A1: Pre-engineered building fabrication is a construction method where building components are designed and manufactured in a factory setting before being assembled on-site.
Q2: What are the main advantages of using pre-engineered buildings?
A2: The advantages include reduced construction time, lower overall costs, improved quality control due to factory production, flexibility in design, and minimized on-site labor.
Q3: What is the process from design to installation in pre-engineered building fabrication?
A3: The process typically involves:
- Design: Collaborating with architects and engineers to create detailed plans.
- Fabrication: Manufacturing components in a controlled factory environment.
- Transportation: Delivering the pre-fabricated components to the construction site.
- Installation: Assembling and erecting the building on-site, which includes putting together the pre-engineered parts.
Q4: How does Rashian Technologies enhance the pre-engineered building process?
A4: Rashian Technologies enhances the process by offering state-of-the-art design software, precision manufacturing techniques, and expert installation services, focus on quality, innovation, and efficiency.
Q5: Are pre-engineered buildings customizable?
A5: Yes, pre-engineered buildings are highly customizable. While they use standardized components, they can be designed to meet specific requirements for different applications, such as warehouses, industrial facilities, or commercial spaces.
Q6: What types of projects are suitable for pre-engineered building fabrication?
A6: Pre-engineered buildings are suitable for a wide range of projects, including industrial facilities, warehouses, retail stores, office buildings, and agricultural structures.
Q7: How long does it take to complete a pre-engineered building project?
A7: The timeline can vary depending on the project’s complexity and size. However, pre-engineered buildings generally have a shorter construction timeline compared to traditional methods due to the efficiency of the fabrication and assembly processes.
Q8: What are the cost considerations for pre-engineered buildings?
A8: Costs can vary based on the size, complexity, and customization of the building. Often it is cost saving through reduced construction time and labour.
Q9: How do I get started with a pre-engineered building project?
A9: To get started, consult with a pre-engineered building specialist or company like Rashian Technologies.
Q10: Can pre-engineered buildings be expanded or modified in the future?
A10: Yes, pre-engineered buildings can be designed with future expansion or modification in mind.
Q11: What is pre-engineered building fabrication?
A11: Pre-engineered building fabrication involves designing and manufacturing building components off-site in a factory setting.
Q12: What are the key stages in the pre-engineered building process?
A12: The key stages include initial design and planning, fabrication of building components, transportation to the site, and on-site assembly and installation.
Q13: How does pre-engineered building fabrication benefit the construction process?
A13: It offers benefits such as reduced construction time, lower costs, enhanced quality control, and increased flexibility in design. It also minimizes on-site labor and disruption.
Q14: What role does Rashian Technologies play in pre-engineered building fabrication?
A14: Rashian Technologies provides advanced solutions and expertise in the design, fabrication, and installation of pre-engineered buildings, ensuring high quality, efficiency, and adherence to industry standards.
Q15: How can I get started with a pre-engineered building project?
A15: Start by consulting with a pre-engineered building specialist or company like Rashian Technologies to discuss your project requirements, obtain a design proposal, and understand the fabrication and installation process.
13 comments on “From Design to Installation by PEB”
Comments are closed